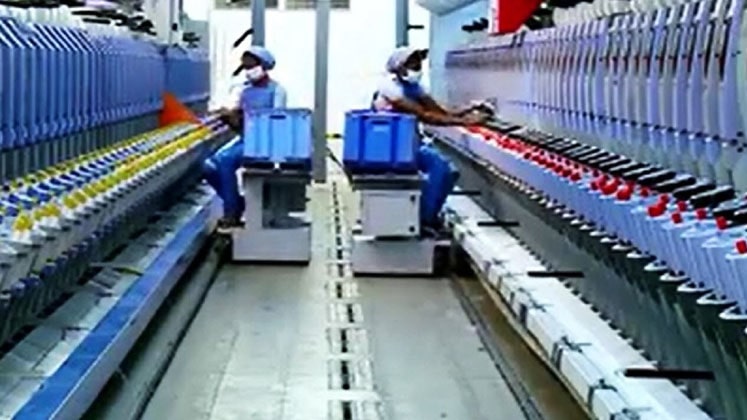
The textile and garment sector in Bangladesh has adopted new heat recovery technologies to utilise waste heat energy from gas burners installed to run the factories even as large number of big weaving, washing and spinning mills have adopted these new technologies for green transformation while also maintaining the business competitiveness.
Media reports maintained this while adding that the waste heat recovery system offers textile mills an economic and green solution to save valuable energy even as they underlined that earlier, the burner exhausts used to be released in the air but now the millers capture it to run air conditioning, boil water and other purposes, thereby enabling them to save both energy and money.
According to the PaCT or the Partnership for Cleaner Textile (launched in 2013, PaCT is a programme led by International Finance Corporation, IFC, which focuses on reducing the environmental impact and resource consumption of Bangladesh’s textile sector), the new system (recovery technologies to utilise waste heat energy) extracts and reuses waste energy from industrial processes instead of dissipating it into the environment and more than 338 factories were using the waste heat recovery systems, which the PaCT underlined, helped reduce gas consumption by 1.26 per cent to 12,74,983 cubic metres from 12,91,122 cubic metres, annually.