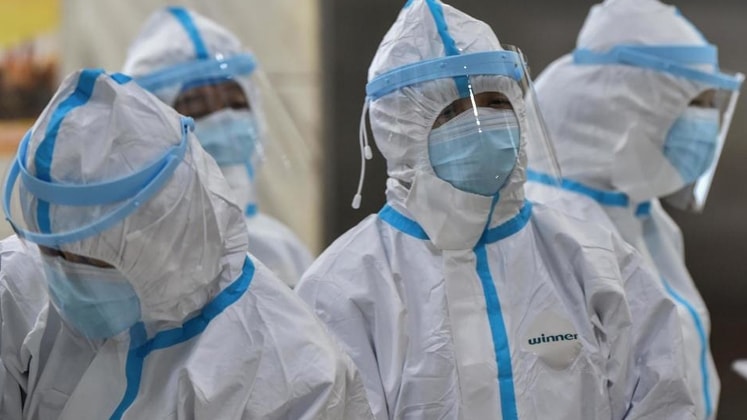
Bangladesh has around 102,927 registered doctors and 56,734 nurses across the country, as per the Bangladesh Medical and Dental Council and the Bangladesh Nursing and Midwifery Council. Apart from them, every hospital has ward boys, security personnel, administrative officials and employees at other departments — the total number of whom, though significant, is currently unavailable.
Ever since the detection of first coronavirus positive case in the country – which till the time of filing of the report had touched 88 with nine reported deaths – these medical and paramedical professionals are at the forefront of Bangladesh’s fight against the dreaded COVID-19.
Notorious for being extremely contagious, hospitals have dedicated and separate isolation units for possible coronavirus patients to ensure that the dreaded virus is not spread among other patients. But those treating them are also at increased risk of getting infected, to prevent which, doctors and nurses need Personal Protection Equipment (PPE) to shield them from COVID-19. However, with the number of positive cases increasing significantly in Bangladesh as well as other countries that are now fighting against coronavirus, the demand for PPE is also on the rise.
Rising to the occasion, the garment manufacturers of the country have now joined hands to manufacture PPE, which are classified into four different categories. According to the World Health Organisation, the four categories of PPE are respectively the full-face or half-mask, air-purifying respirator (level 1); chemical resistant clothing – one-piece coverall, hooded two-piece chemical splash suit, chemical resistant hood and apron, disposable chemical-resistant coveralls – (level 2); gloves, outer and chemical resistant (level 3); and gloves, inner and chemical resistant (level 4).
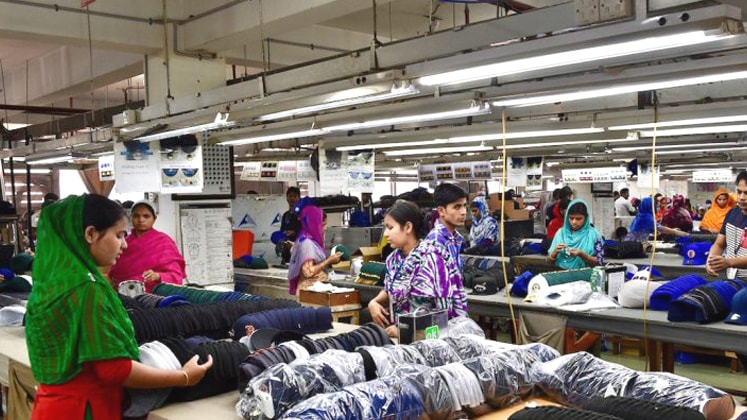
The production of PPE in Bangladesh got a further boost after the country’s Government approved a joint initiative – Pay It Forward, the Manush Manusher Jonno Foundation, the Bangladesh Garment Manufacturers and Exporters Association (BGMEA), British retail giant Marks & Spencer, the Arunachal Trust, and the BUET Alumni Association – on design and fabric developments. Around five manufacturing units namely Urmi Group, Snowtex, Aman Group, Dekko Group and Smartex Group have already started production of PPE.
“We would not make any profit from making the PPE because people need the safety gears urgently. We will only take fabric charge as we will have to buy the raw materials.” Asif Ashraf, Managing Director, Urmi Group
At the same time, Snowtex is planning to initially start with production of 50,000 pieces of PPE, which will be increased later on. “We will produce 50,000 pieces initially, of which, we will distribute 17,000 pieces free of cost,” added SM Khaled, Managing Director of Snowtex.
Another 12 textile companies have also reportedly started production of PPE for the local markets while also looking to export overseas including to countries like the USA, Kuwait, Sri Lanka and Nepal.
“Four countries have already sent their demand letters to Bangladesh for sourcing high-quality PPE. But our textile mills can only manufacture the chemical resistant clothing (level 1/2) right now,” shared Safiul Islam Mohiuddin, lawmaker from the ruling party of Bangladesh and former President of the Federation of Bangladesh Chambers of Commerce and Industries (FBCCI).
“Local manufacturers have already sought the World Health Organisation’s technical collaboration for meeting the standard of professional and medical PPE,” informed Navidul Huq, Director of Niche Stitch Ltd, adding that procurement of raw materials for specialised fabrics is the main challenge currently. “With proper training and expertise, we can make and export it worldwide,” Navidul claimed.
Meanwhile, Denim Expert Limited, another leading garment manufacturer of the country, has offered to manufacture protective face masks and PPE on a non-profit basis to help tackle the global pandemic. Mostafiz Uddin, Managing Director of the company, has already reached out to the global community including brands and retailers, governments, embassies, donors, development agencies, global apparel associations and bodies in this direction.
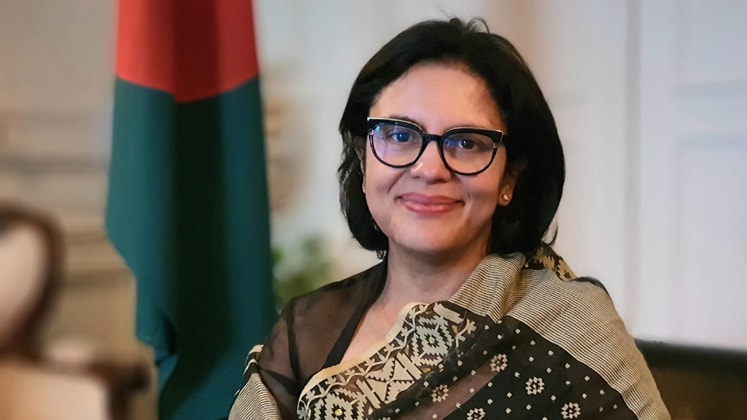
“The world is facing a grave threat, and we all need to play our part. My question is – how can we help? Now is not the time for profiteering. Now is the time to tackle this crisis together. That’s why I am making this offer to work on a not-profit basis at this critical time. We have the production capacity, we have the skills and know-how, we have the people. My business will not make a penny out of this. We all have a responsibility and role to play at this critical situation. It’s time not to consider who is big or who is small. I request all to come forward from their respective positions to contribute to improve the situation,” observed Mostafiz.
“Our ultimate goal is to export PPE to the rest of the world and we want to do it very fast. As soon as we can get the certified fabric, we will be switching to certified and imported fabrics for our PPE. This is an ongoing process; every day new factories are joining with notable efforts. We have factories donating stitching capacity, fabrics and fund for buying fabrics every day.” – Rubana Huq, President, BGMEA
Rubana also added that the apex garment exporters’ body is in a discussion with ILO, WHO, WFP, UNICEF and other organisations and seeks help from them to expedite the process of converting production capabilities available in Bangladesh to produce PPE.
The traders’ body is alternatively sourcing fabric from China which currently has a lead time of 15-20 days because of severe delays in air freight routes.