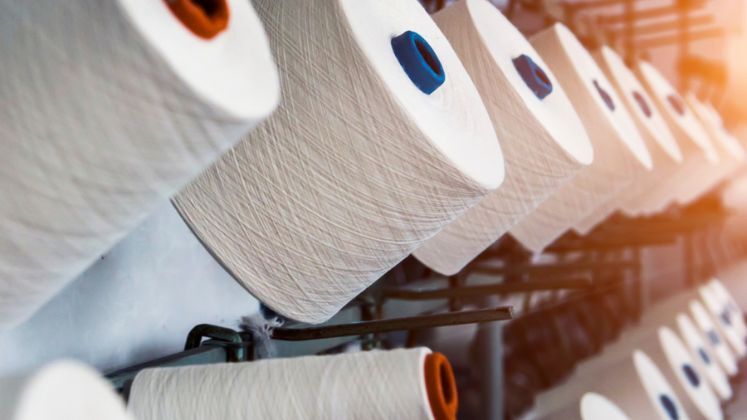
Bangladesh’s textile industry, a vital component of the nation’s economy, is increasingly reliant on imported yarn and fabrics, particularly among knitwear manufacturers, despite substantial local investments aimed at boosting production capacity. Recent data from the National Board of Revenue reveals a concerning trend: cotton yarn imports skyrocketed by 39 per cent in 2024, amounting to a record US $ 2.28 billion, while fabric imports for knitwear factories surged by 38 per cent, costing an additional US $ 2.59 billion.
The majority of these imports are sourced from India, intensifying competition for local suppliers. This shift comes as the industry grapples with rising production costs and diminishing Government incentives for using domestic yarn. In the wake of the Covid-19 pandemic, local textile millers invested approximately US $ 2 billion to expand their capabilities, but many now find these investments strained as they face challenges in maintaining price competitiveness.
The preference for imported materials is largely driven by cost considerations. For instance, the price of recycled polyester cotton imported from India is US $ 2.19 per kilogram, while local spinning mills charge around US $ 2.45 for the same material. This price disparity has led to a dramatic increase in imports; while MB Knit Fashions previously sourced 20 per cent of its yarn from abroad, that figure has now risen to nearly 90 per cent.
Despite these alarming trends, the Bangladesh Textile Mills Association (BTMA) does not currently track the decline in local mills’ sales. However, it notes that two years ago, domestic mills supplied approximately 85 per cent of the yarn used in knitwear exports.
Local textile mill owners report that production costs have surged by 30 per cent over the past two years, driven by escalating gas prices, increased wages, and reduced gas supply. These rising costs, combined with reduced Government incentives—cash incentives have plummeted from 4 per cent to 1 per cent and special incentives from 1 per cent to 0.3 per cent—have made it increasingly difficult for local mills to compete. The lengthy processing times for these incentives further discourage garment exporters from opting for local yarn.
Additionally, concerns over illegal yarn imports through smuggling and the misuse of bonded warehouse privileges have flooded the market with cheaper alternatives. As local mills struggle to maintain profitability, more than 30 textile mills have reportedly shut down in the past year, with many others operating at significantly reduced capacity.
The competitive landscape is further complicated by India’s advantages in textile production, including its access to domestic cotton supplies and Government support for its textile exporters. Indian textile manufacturers benefit from various financial incentives, such as the Remission of Duties or Taxes on Exported Products (RoDTEP), which provides exporters with a rebate of up to 3.88 per cent of the export value, in addition to a 2 per cent duty drawback on textile exports. These advantages enable Indian exporters to offer lower prices, raising concerns among Bangladeshi producers about potential dumping practices.
Experts suggest that rather than relying on direct financial aid to support the textile sector, efforts should focus on reducing overall business costs, including logistics, banking, and customs fees, to enhance Bangladesh’s competitiveness in the global market. As the country prepares to graduate from its Least Developed Country (LDC) status, long-term sustainability in the textile industry will depend on addressing these systemic challenges.